
Predictive Maintenance & the Transformation S-curve: Don’t Forget Context
With all the promised value around IIOT and predictive maintenance (PdM) and the key role they play in Industry 4.0, you may be gearing up to instrument your critical equipment with sensors. That’s definitely an important step, but if you’re missing several essential prerequisites, your ROI may be a lot further away than expected.
Remember the transformation S-curve
All technological transformations follow S-curves. Until you reach a critical transformation level, ROI will be zero—but getting to that critical point is often a slow process.
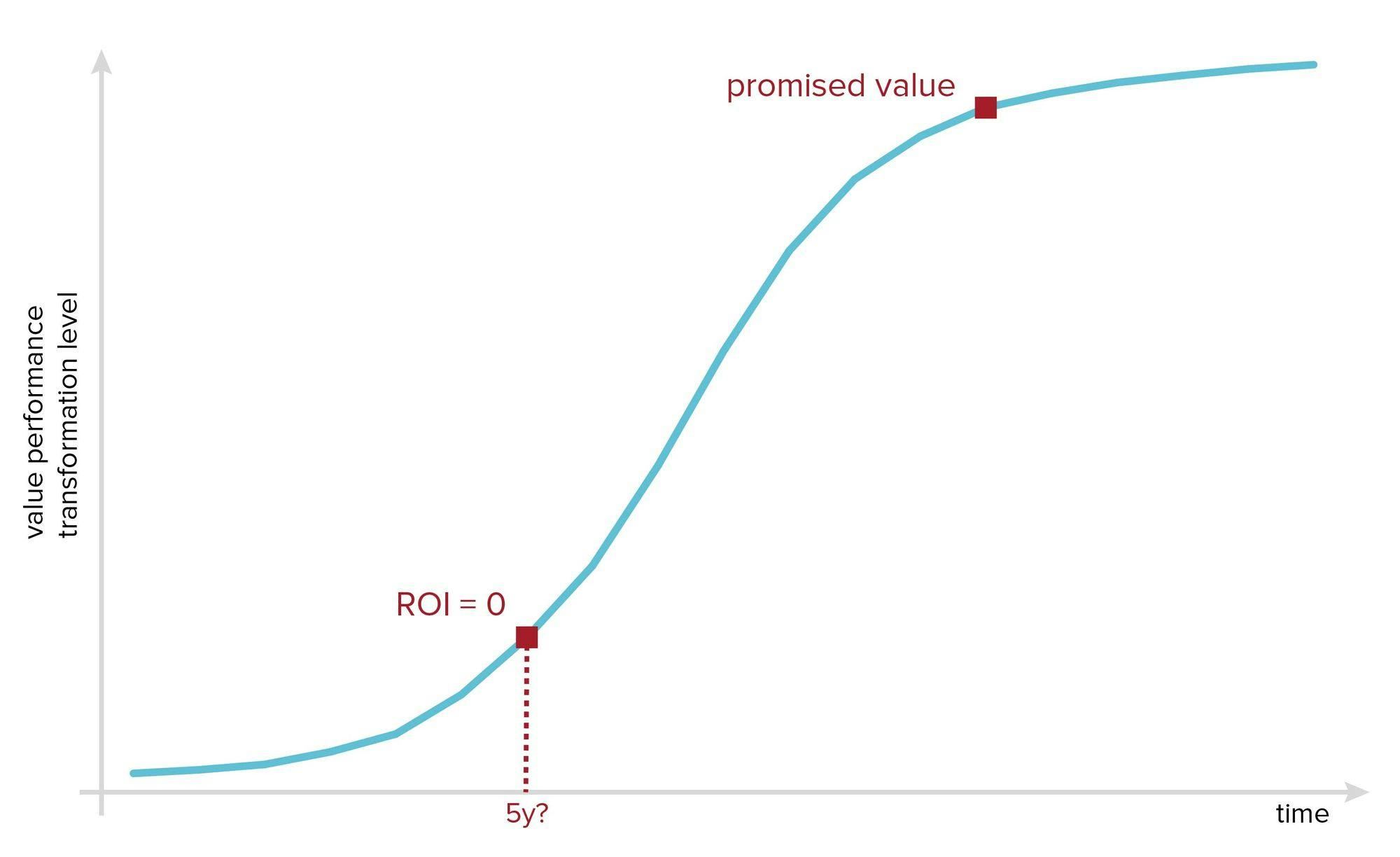
ROI for your sensors will be zero until you reach a critical transformation level
When it comes to facility maintenance planning, sensors are often directly tied to the ultimate goal, the promised value: avoiding surprise plant shutdowns due to sudden equipment failure or, worse, a catastrophic disaster that throws your business into a slew of global, negative press.
But you can’t just immediately skip ahead to promised value.
Imagine this: Your predictive algorithms just picked up an anomaly from a vibration sensor on a compressor. It may fail, and you’d better fix it quickly. No problem, because you’ve been alerted early and mobilize your maintenance team to deal with it. Except...what parts do they need to fix it? What linked equipment do they need to shut down? They’re missing the context to effectively deal with the problem. Manually sifting through hundreds of scanned documents to gather that context will take time you don’t have.
“If the hierarchy is not accurate it is impossible to gain the reliability, maintainability and required traceability of the assets. How can Planners do their job if they are not aware of the plant’s assets and in particular how the assets relate to other assets?” - Paul Langan
If you don’t get that contextual information down, your sensors provide little value. All the investment you poured into your PdM initiative just went down the drain, and you’re back to square one.
Maximizing maintenance ROI: Precursors to IIOT
So how do you avoid potential disaster and find that context to make your IIOT investments worthwhile? Here are some key steps:
- Build a hierarchical asset register that complies with a standard such as ISO 14224:2016. You will need to retrieve and classify data from engineering drawings and reports to do so.
- Generate Bill of Materials. You will need to find and retrieve data residing in lots of tables in scanned documents, normalize part names, etc., to achieve this.
- Develop a maintenance plan running ECA, FMEA, and analyses of backlogs, spare parts, costs, and so forth.
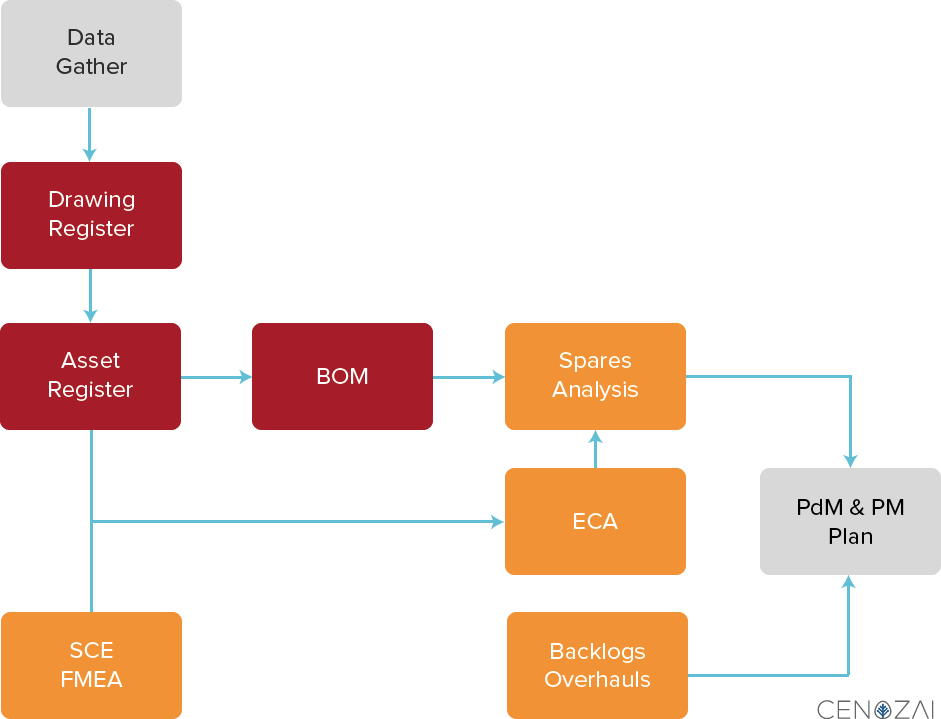
Key steps to gathering context for your facility maintenance plan
Gathering context with machine learning
The data needed to establish context typically sits in tens of thousands of scanned documents. Currently, many businesses are trying to achieve this through tedious manual effort to complete the task. With time and costs piling up, promised value isn’t even in sight anymore.
But there’s a much more efficient way, through an ensemble of computer vision and natural language understanding tools that can significantly cut time and cost to reach your goals. For example, machine learning algorithms can parse and classify huge volumes of unstructured documents to help you access the most important drawings first, like P&IDs. Other algorithms can then come in to detect, OCR, and identify equipment, lines, instruments and their loops, and other key information from those P&IDs. Perhaps you also want to run a root cause analysis to quantitatively understand equipment interactions in the failure of a processing unit.
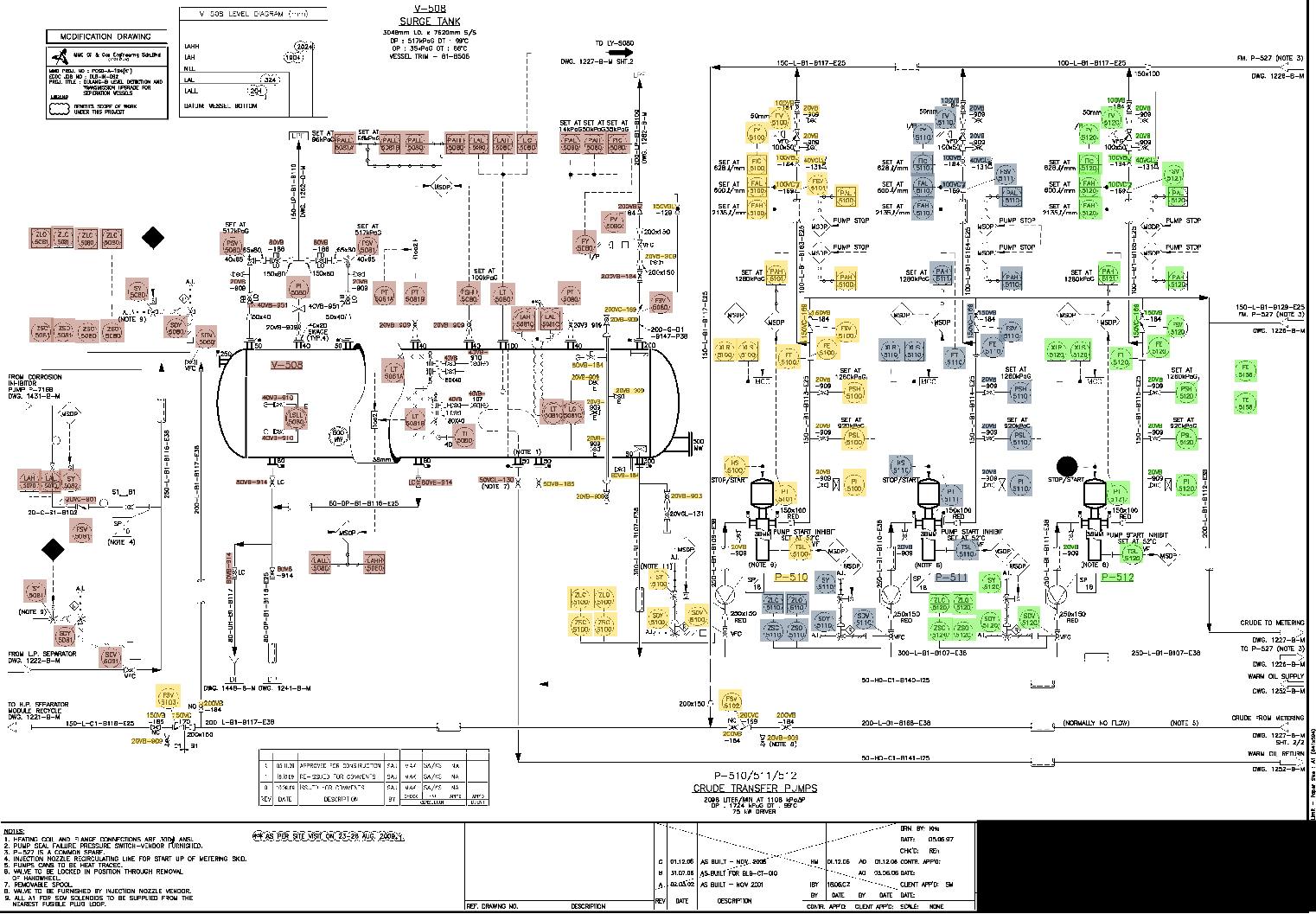
Use Cenozai’s Facility Maintenance system of intelligence to automatically capture and connect equipment and tag IDs, then organize them in an ISO 14224:2016 compliant hierarchy.
With machine learning powering your team’s efforts to gather context and tie it into your predictive maintenance plans, the gains are significant:
- Improved purchase planning for spare parts and inventory.
- Improved preparation when on the job. You understand which parts to bring for the fix, and can minimize shutdown to only the necessary systems.
- Improved maintenance planning working in tandem with PdM. Perhaps you technically only need to shut down the system to fix broken equipment A, but because you’re armed with the physical context of all the various equipment throughout your systems, you realise you might as well upgrade equipment B to minimise losses during downtime.
Seamless systems of intelligence
You still need to bring a human into the loop, though. No machine learning algorithm can perform at 100% accuracy—if someone tells you otherwise, it’s snake oil and you should stay far away from that person. Still, machine learning should certainly be able to take you more than 90% of the way. For the information that requires 100% accuracy, a human needs to come in to make corrections.
It can be tricky to make sure you’ve pieced together the right algorithms, along with the correct intermediate data pipeline, and pleasant user interface for remediation. A system of intelligence can help you overcome that.
Cenozai has developed a system of intelligence for facility maintenance planning powered by a combination of domain expertise, deep learning algorithms, and human-in-the-loop machine learning to deliver a seamless experience to your facility management team. The combination of these techniques and finely tuned workflows allow you to organize your preventive maintenance (PM) and PdM plans, predict gaps and waste in current plans, and quantitatively analyze complex systems. Check out Cenozai's AssetBot and Advanced Engineering Search solutions, or contact us at hello@cenozai.io to learn more.
Recommended Posts
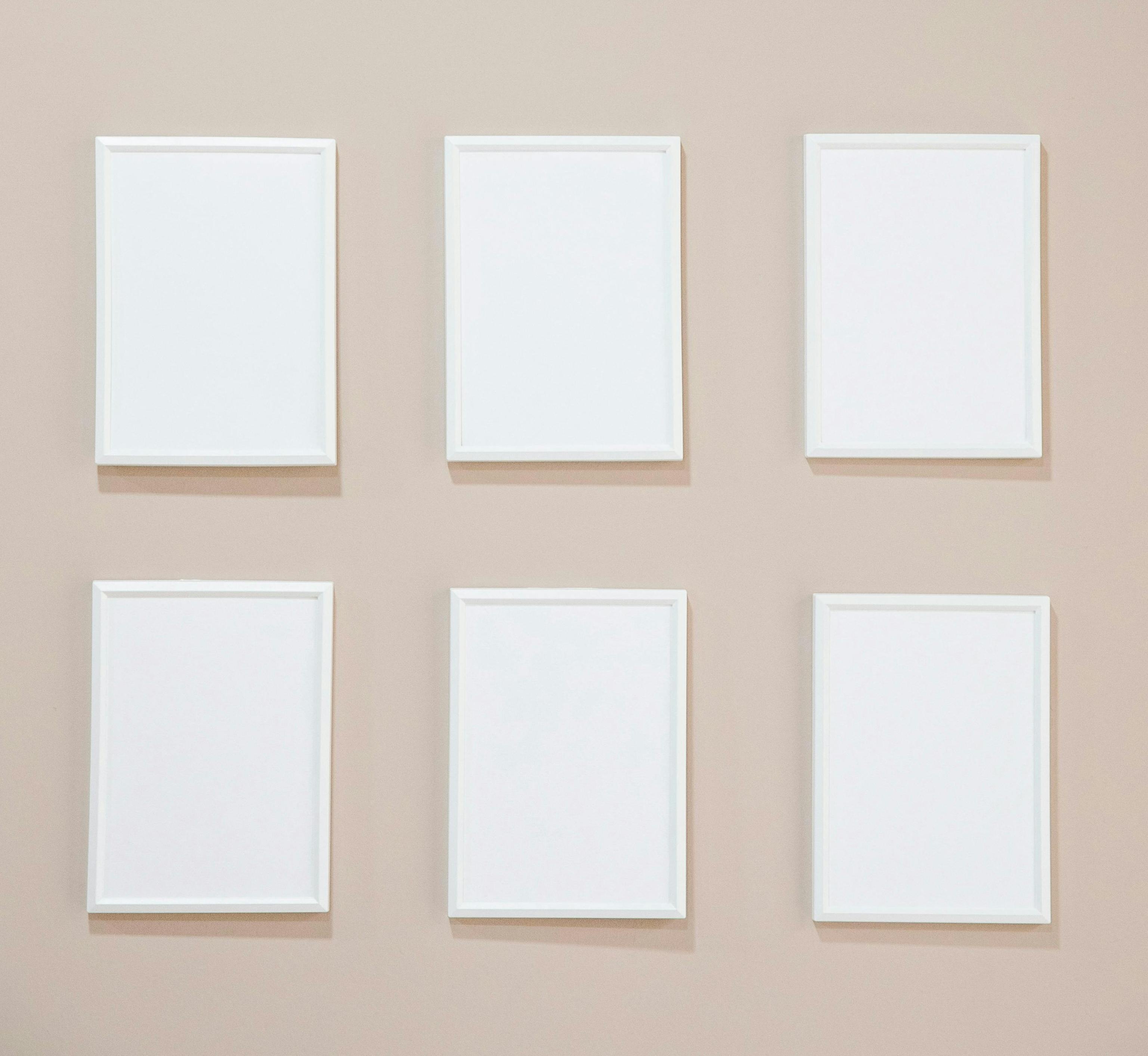
8/15/2024
A new era of enterprise search for facilities
(Part II): Data preparation
Before implementing new search technology, data cleanup and preparation is critical. Here's what you need to do.
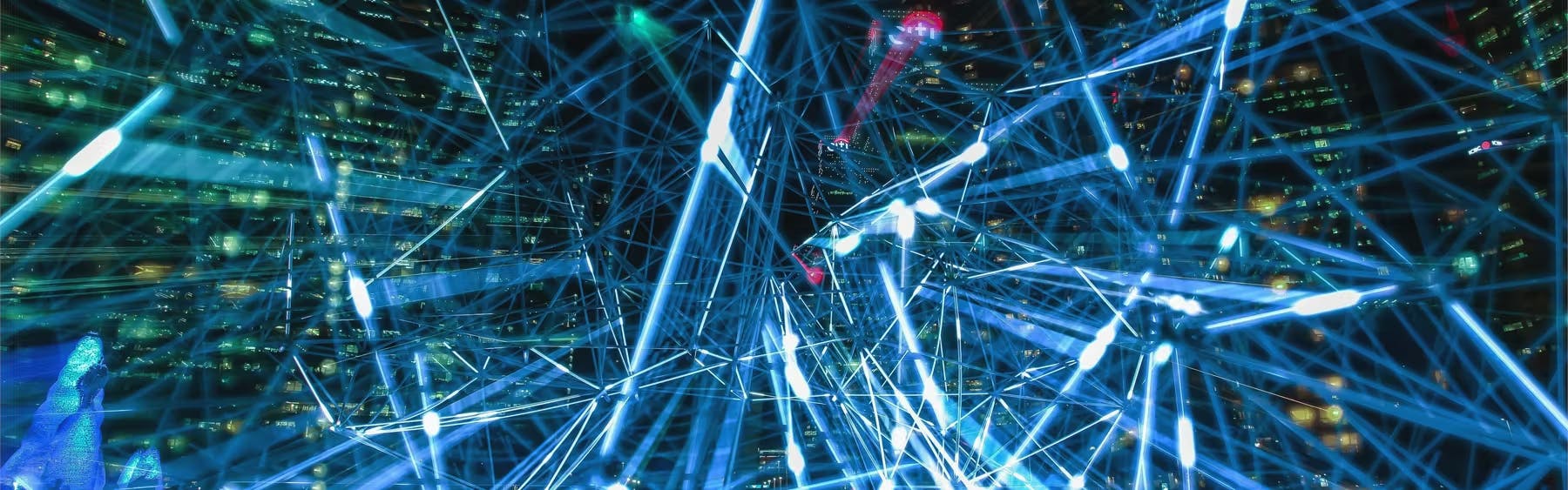
8/1/2024
A new era of enterprise search for facilities
Enterprise search is changing for facility operators—out with the file hierarchies and in with the information networks.
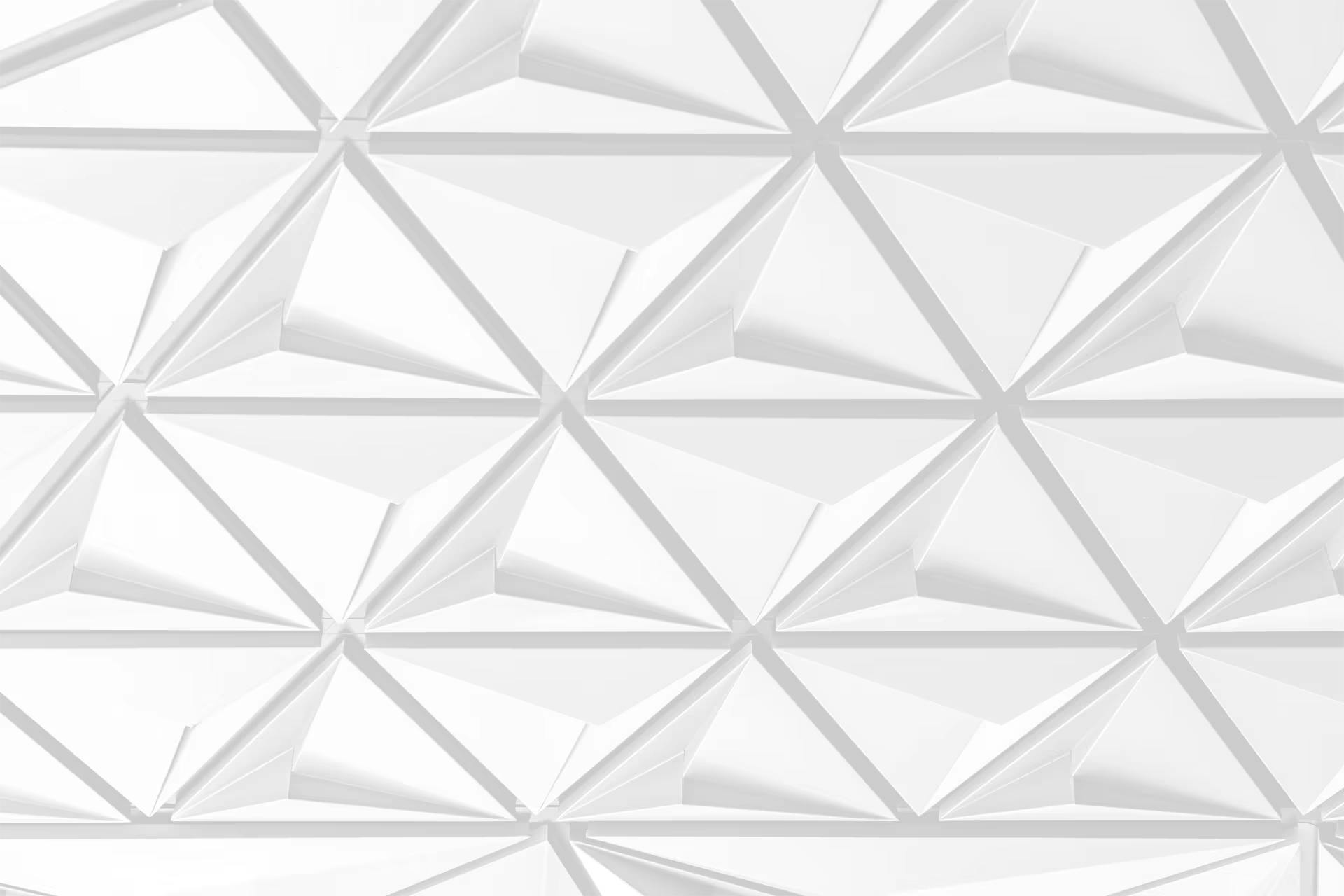
12/16/2022
Industry 4.0: The Unstructured Data Perspective
How to build a contextual platform that will be the launching pad for every one of your Industry 4.0 initiatives.